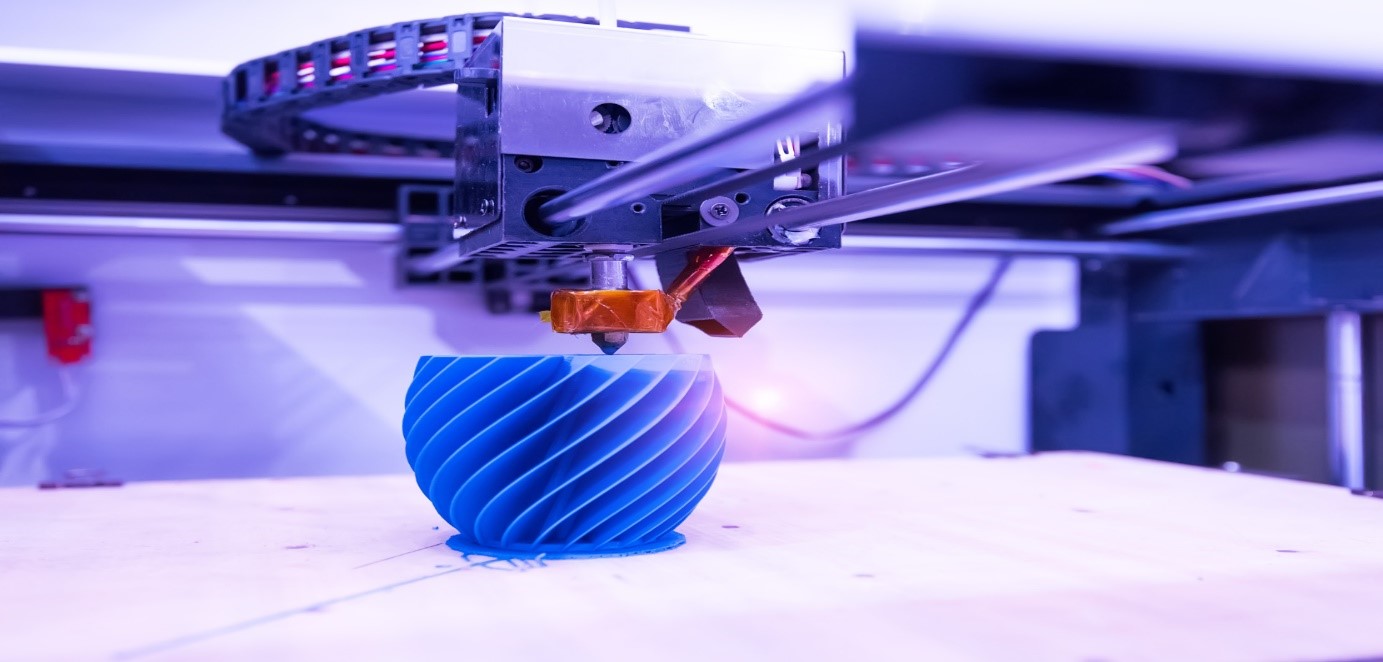
The Devastating Impacts of COVID-19 Pandemic to Manufacturing Organizations
Organizations throughout the world are facing arduous disruptions in various forms that often threaten their endurance and functionality. These include natural disasters, pandemics, economic crisis, political turmoil, technological change and many other types of adversities resulting in vulnerable conditions that necessitate the firms to be resilient. Beyond the kinds of disruptions that the firms have gone through, the COVID-19 pandemic has imposed a brand-new devastation that severely impacted the organizations across the board. It has resulted in a major downturn of economy and unexpected transition in the way of operating businesses. In a swift speed, online learning, virtual conferences, webinars and online meetings have emerged as the new norms in organizations around the world. Lockdowns, movement control orders and social distancing have impacted many organizations, particularly those operating in manufacturing sector.
The manufacturing sector is highly impacted due to the supply chain disruption at large as a consequence of lockdowns and international border closures, which have impeded the transportation of materials and goods. Additionally, the efficiency based physical layout in the production floors and operation areas as well as the lack of technological advancement to support operational flexibility have also inhibited social distancing practices in numerous manufacturing organizations. Failure to adapt to the new norms and lack of resilience have imposed severe challenges to the organizations that caused detrimental implications such as layoffs, temporary closure and even total shut down of the firms globally. This begs for attention towards preserving resilience as it is the key that allows organizations survive challenges and adapt to the unexpected changes in the environment.
Organizational Resilience: AM as a Potential Driver
Organizational resilience is an integral capability of firms to withstand challenges and remain competitive in volatile environments. Organizational resilience is defined as “the maintenance of positive adjustment under challenging conditions, such that the organization emerges from those conditions strengthen and more resourceful”. It is a desired capability of organizations that had gained remarkable attention due to its potential contribution in ensuring firms’ performance and competitiveness in both predicted or unpredicted situations.
Organizational resilience can be associated with various types of tangible and intangible resources of an organization. In this line, the ability to adapt to the emerging technologies is vital to enhance organization resilience among manufacturing firms as a way to minimize the impacts caused by COVID-19 pandemic. The emerging technologies introduced by Industry Revolution 4.0, particularly, Additive Manufacturing (AM) appears to be a potential technology that can promote resilience of manufacturing firms in dealing with challenges imposed by the COVID-19 pandemic.
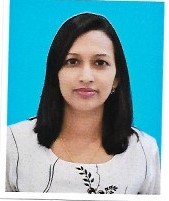
Shela Vengirasamy is currently pursuing her PhD in the School of Management, USM, Penang. Her area of study is Management and Organizational Behavior. By profession, she is currently an Administrative and Diplomatic Officer in the public sector of Malaysia. She has a vast experience in both public and private sector. She started her career in a reputable manufacturing-based multinational corporation (MNC) and extended to serve the nation through the public sector. She possesses both local and international working experience by serving different departments and ministries throughout her career.
Email: vshela34@gmail.com
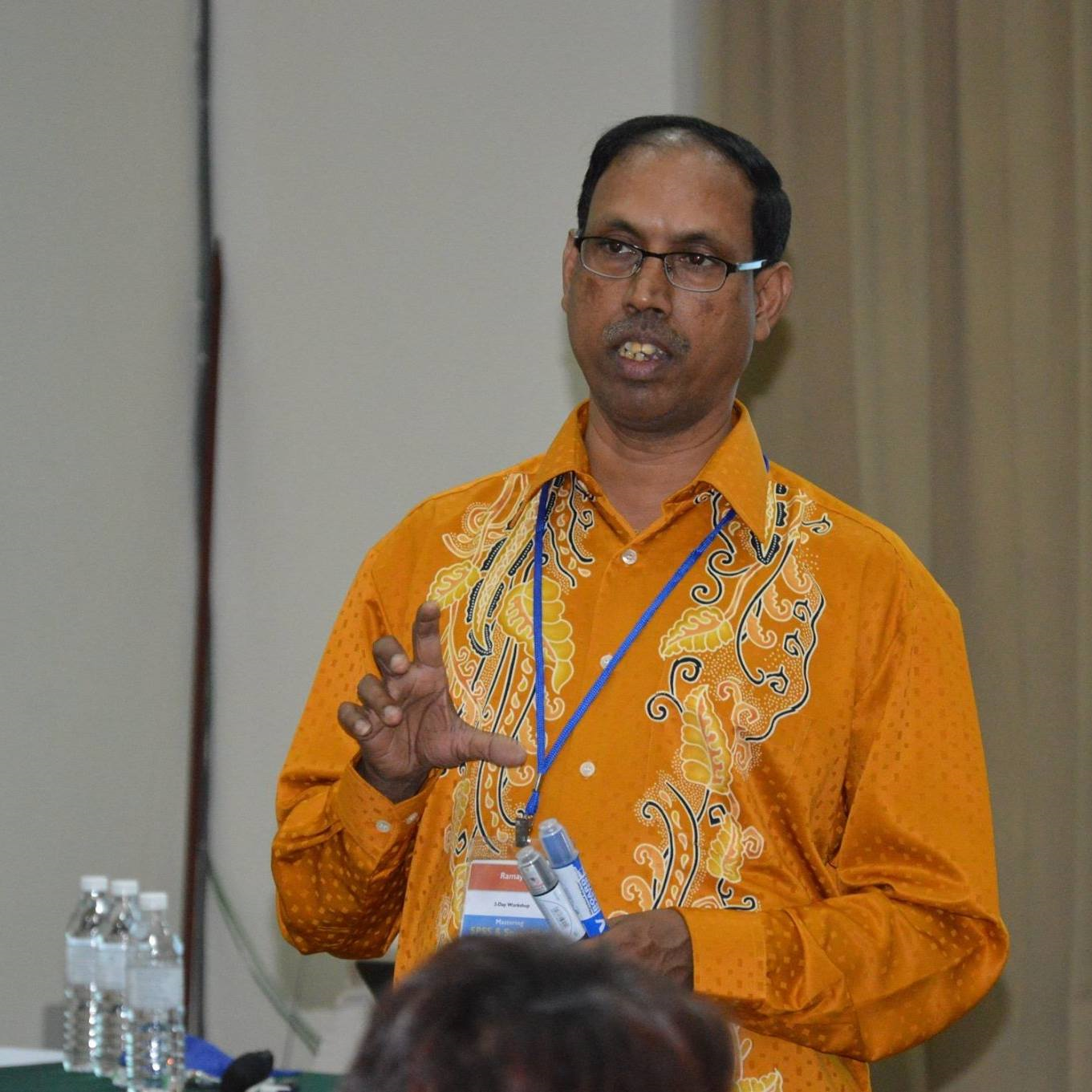
T. Ramayah, is currently a Professor of Technology Management, School of Management, Universiti Sains Malaysia, Adjunct Professor at Azman Hashim International Business School (Malaysia), Daffodil International University (Bangladesh) Sunway University (Malaysia), Universitas Indonesia, (Indonesia), Chandigarh University (India) and The University of Jordan (Jordan). He is currently the Chief Editor of the Asian Academy of Management Journal and Journal of Applied Structural Equation Modelling. His publications have appeared in various high impact journals. His full profile can be accessed from http://www.ramayah.com
Email: ramayah@usm.my
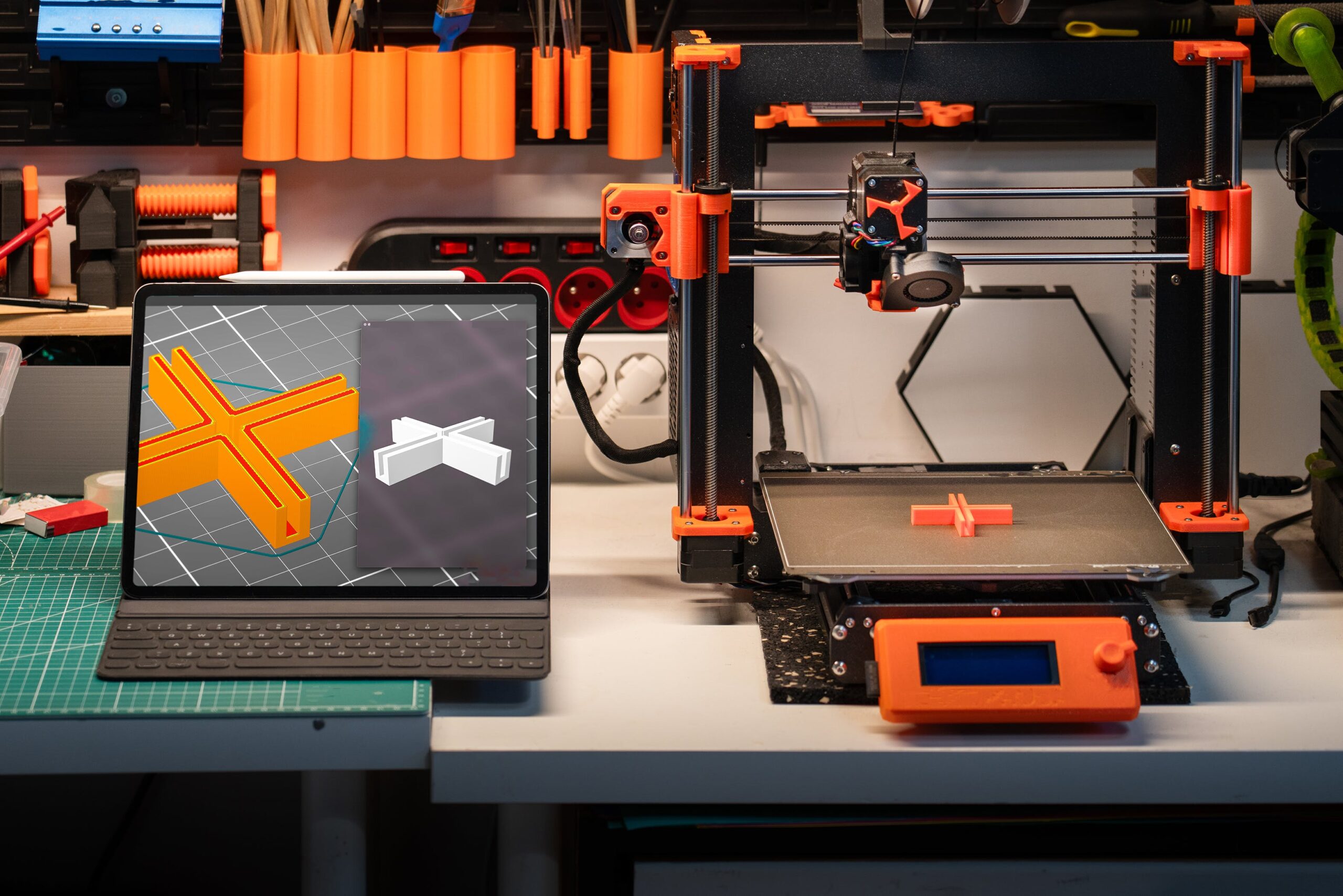
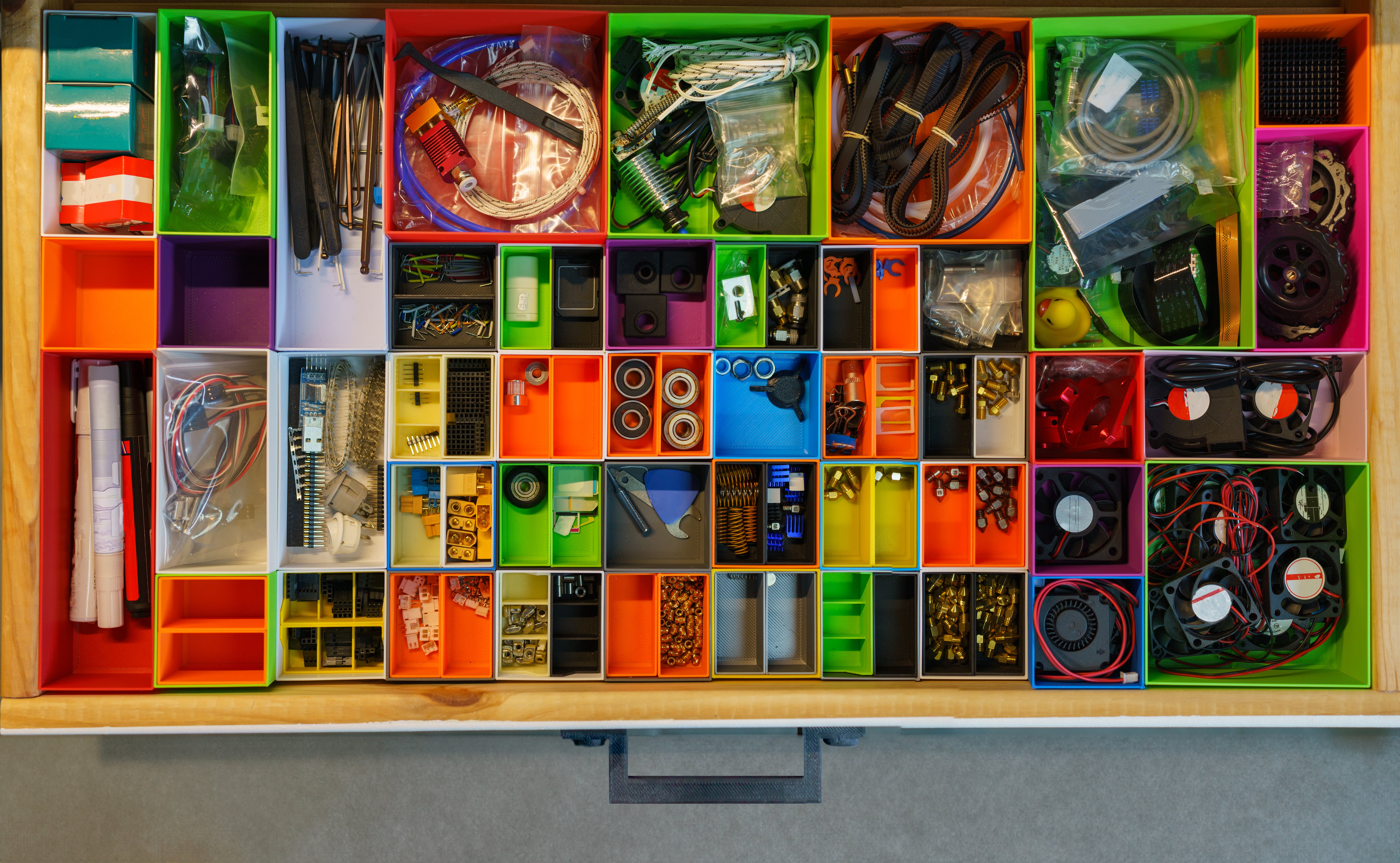
AM, which is also known as 3D printing is defined by the American Society for Testing and Materials (ASTM F2792) as “the process of joining materials to make object from 3D Model data, usually layer upon layer, as opposed to subtractive manufacturing methodologies, such as traditional machining”. Raw materials such as metal, thermoplastics, bio chemical, ceramics or other types of materials are used in the forms of liquid, filament, powder or solid layers to print the products. The primary technologies applied in AM are Stereolithography, Selective Laser Sintering, Fused Deposition Modelling, Inkjet Printing, Direct Metal Laser Sintering, Poly-Jet 3D Printing, Color-Jet -Printing, Laminated Object Manufacturing, Electron Beam Melting and Multi-Jet-Printing.
Regardless of the technologies or materials used, the general processes involved in AM are: (1) designing parts using software, (2) importing the digital file to the 3D printer, (3) printing the physical part using materials, (4) cleaning and strengthening the part . The products produced via AM technology varies, ranging from small products such as handicrafts, medicines, utensils up to homes. AM is able to build complex shapes by adding thin layers, which is nearly impossible to be produced by traditional manufacturing. Moreover, it prints out products without using any specific tooling as the conventional manufacturing does. It replaces the lengthy processes of conventional manufacturing such as cutting, drilling, milling, molding, joining and fixing the parts with a highly flexible and efficient method.
One of the most significant advantages of AM that can be leveraged to deal with the new norms imposed by COVID-19 pandemic is the manufacturing flexibility that allows decentralization of production. In other words, AM restructures the supply chain and logistical aspects by renewing business models of manufacturing organizations through its capability of processing numerous materials by remote. Hence, in the current disruption caused by COVID-19 pandemic, this technology can be utilized for localizing manufacturing of products at distinct locations. Such advancement brought by AM will effectively help to reduce the risk associated with supply chain disruptions in the manufacturing sector.
For instance, a product designed in the U.S can be produced (i.e., printed) on-site, which is closer to the customers. This reduces the need for transportation and unnecessary movements, which has become a major concern during the pandemic condition. By providing opportunities for decentralization and flexible manufacturing, AM technology certainly supports social distancing, which is nearly impossible in traditional manufacturing. Thus, the application of AM has a high potential to escalate organizational resilience of manufacturing firms during disruptive conditions, more specifically, during COVID-19 pandemic, which has an undefined ending date.
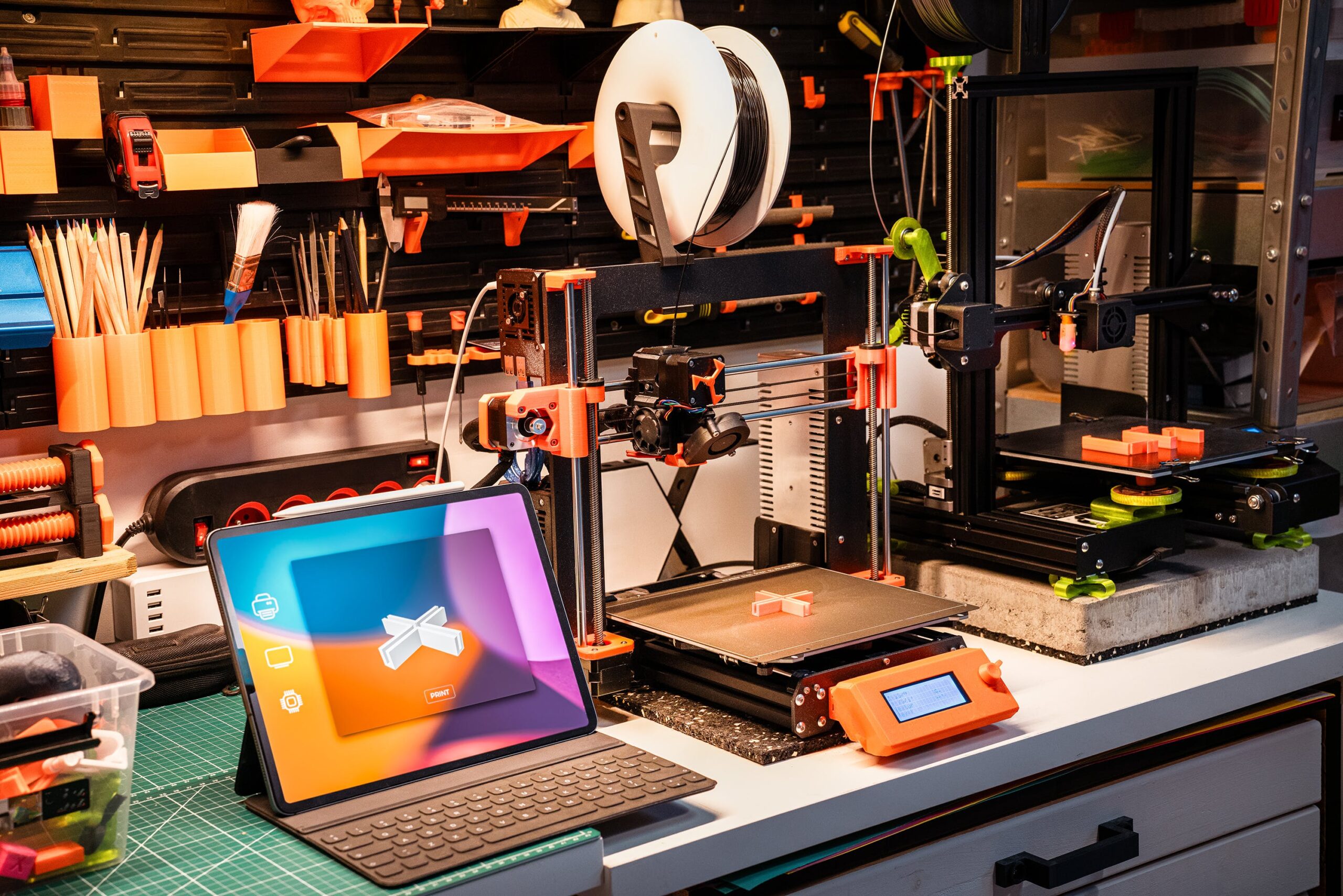
In addition to that, it also provides various benefits to the firms as it allows design freedom and customization of products, cost efficiency, demand-based production, shortened delivery time as well as reuse of the materials. It is argued that AM process would be able to reduce materials waste up to 90% and reduce the assembly time by 50%. This induces competitive advantage to the organization and further enhances its resilience. In the same vein, the efficiency of AM in energy consumption, waste management and refurbishment that leads to social and environmental sustainability may assist in augmenting the brand name and reputation of an organization. Furthermore, AM feature that allows customer involvement at product design level may also increase the marketability of the organization’s products. All these attributes are highly supportive to amplify organizational resilience during COVID-19 pandemic, which is not only limited to surviving but also to thrive in adverse conditions and to appear more successful.
Conclusion
AM has all the potential to become the mainstream manufacturing process concurrent with the Industry Revolution 4.0. It is capable of restoring robustness to manufacturing organizations and exacerbate the organizational resilience of the sector to the next level irrespective of the pandemic situation. However, it needs momentous commitment and acceptance of the top management to implement this technology towards improving competitiveness and organizational resilience as a whole. Hence, AM should not just be perceived as an alternative method or a prototyping procedure for the sake of research and design purpose. Rather, it’s potential should be fully utilized to set manufacturing organizations free from impediments caused by COVID-19 pandemic as well as any forthcoming disruptions that may threaten the competitiveness of the organizations.